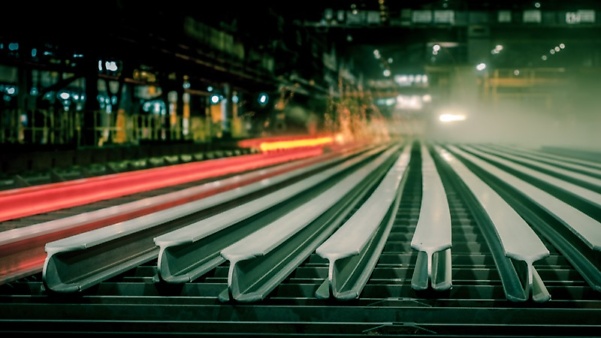
Wie unser Stahl entsteht: Das Profilwalzwerk.
In der Formstahlstraße wird Stahl zum Profil.
Die technologische Linie unseres Walzwerkes beginnt am Erwärmungsofen. Die Beam Blanks, also die Vorblockprofile aus dem Elektrostahlwerk, können dem Ofen in direkter Linie mit Restwärme aus der Stranggießanlage oder im kalten Zustand aus dem Lager zugeführt werden. Im erdgasbeheizten Ofen werden die Beam Blanks auf Temperaturen von 1.250°C erwärmt. Nach der Entnahme aus dem Ofen wird der Beam Blank in einem Zunderwäscher mittels Hochdruckwasser von oxidierten Anhaftungen befreit. Anschließend werden die Beam Blanks dem Walzprozess zugeführt.
Er wird in unserer Formstahlstraße realisiert, die zu den modernsten Profilstahl-Walzstraßen in Europa gehört. Ihre Kapazität liegt, abhängig von Form und Größe des Profilstahls, zwischen 70 und 200t in der Stunde.
In der Profilwalzstraße werden Stahlprofile im Duo- sowie im Universalwalzverfahren hergestellt. Die Profilwalzstraße arbeitet im Reversierbetrieb. Dabei wird der Profilstab in mehreren „Stichen“ vor- und rückwärts durch die mit Kalibern versehenen Walzen geführt. Alternativ arbeiten die Walzen nach dem Universalverfahren.
Einzelne Walzgerüste geben die Form.
Die Walzanlage besteht aus drei hintereinander angeordneten Gruppen von Walzgerüsten: Einem Vorgerüst, dem sogenannten Break Down, einer Tandem-Zwischengruppe, bestehend aus drei Walzgerüsten, sowie einer Fertiggruppe, bestehend aus zwei Walzgerüsten. Beim Durchlaufen dieser Walzgerüste wird der Querschnitt des Walzstabes mehr und mehr dem Querschnitt des Endproduktes angepasst. Verantwortlich dafür ist die mechanische Verformung in den Räumen zwischen den Walzen, den sogenannten Kalibern.
Im Vorgerüst wird der ursprüngliche Beam Blank zum Vorprofil umgeformt. Dies geschieht in mehreren reversierenden Durchläufen, abwechselnd vor- und rückwärts. Die beiden Walzen des Gerüstes werden von einem Elektromotor mit einer Leistung von 4.400 kW angetrieben. Im Gerüst kann eine maximale Walzkraft von bis zu 10.000 kN realisiert werden.
Auf das Vorgerüst folgt die Tandemgruppe, deren drei Gerüste in kurzen Abständen hintereinander angeordnet sind. Der Walzstab befindet sich während der Umformung gleichzeitig in allen drei Gerüsten. Auch in der Tandemgruppe wird reversierend gearbeitet. Nach jedem Durchlauf wird der Abstand zwischen den Walzen verringert, um eine Reduzierung der Querschnittsfläche zu erreichen. Nach dem letzten Durchlauf gelangt der Walzstab zur Fertiggruppe, in der die geforderten Endabmessungen hergestellt werden.
Durch die ständige Querschnittsverringerung werden aus anfänglich bis zu 11,5 Meter langen Beam Blanks Walzstäbe mit einer Länge bis 100 Metern gewalzt. Im Fertiggerüst erhalten die Stahl-Träger ihre endgültige Form. Die Abläufe in den Walzgerüsten sind grundsätzlich computergesteuert. Somit konzentriert sich die Arbeit unserer Walzwerker heute primär auf Kontroll- und Überwachungstätigkeiten.
Hohe Flexibilität und Leistung dank Umrüstung.
Die Walzen sind unsere Werkzeuge zur Stahlumformung. In unserer Walzendreherei fertigen wir sie aus Walzenrohlingen bis zu einem Gewicht von 22t selbst oder arbeiten die während des Einsatzes an der Walzstraße verschlissenen Walzen nach. Dafür nutzen wir CNC-gesteuerte Walzendrehmaschinen. Gleich neben der Walzstraße befindet sich die Umbauhalle, in der wir die Walzen und Walzgerüste für die folgende Walzung vorbereiten. Damit wir durch schnelle und flexible Umrüstzeiten hohe Walzleistungen erreichen, müssen wir dabei äußerst exakt arbeiten. Wir führen den Gerüstwechsel an allen Gerüstgruppen in einer Zeit von weniger als 20min durch. Bereits kurz nach der Umrüstung wird das neue Profil gewalzt.
Auskühlen und Vermessen.
Nach dem Formungsprozess durchlaufen die immer noch ca. 950°C heißen Walzstäbe eine Messanlage, in der mittels Laser die Geometrie des Profils an mehreren definierten Punkten überprüft wird. Mit einer Geschwindigkeit von fast 10m pro Sekunde passieren die Walzstäbe dieses Profilmessgerät. Auf dem Rollgang vor dem Kühlbett werden sie abgebremst. Dort werden Materialproben für die finale Analyse in den Prüflaboren und in den Werkstätten unserer Qualitätsstelle entnommen. Anschließend werden die Walzstäbe auf das 100m lange Kühlbett geschoben, das die Walzstraße mit der Adjustage verbindet. Durch Hubbewegungen des beweglichen Teils des Kühlbettes werden die heißen Walzstäbe schrittweise über das Kühlbett transportiert. Dabei kühlen sie mithilfe von Luftkonvektion auf Richttemperatur von ca. 80°C ab.
Intensiv geprüfte Stahl-Qualität.
In unserer Qualitätsstelle prüfen wir die einzelnen Materialproben mit unterschiedlichen Beprobungsverfahren. Diese Beprobungen realisieren wir gemäß der geltenden Normen und anhand der individuellen Kundenanforderungen. Von uns eingesetzte Testverfahren sind beispielsweise der Zugversuch und der Kerbschlag-Biege-Versuch. Alle Prüfungen sind Teil unseres zertifizierten und integrierten Managementsystems.