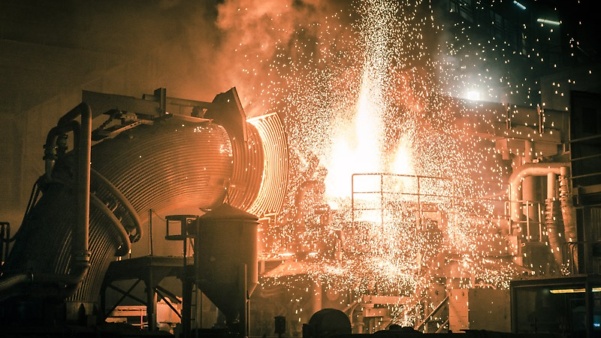
Wie unser Stahl entsteht: Das Elektrostahlwerk.
Ein Lichtbogen schmilzt 135t Schrott zu flüssigem Stahl.
Der vom Schrottplatz kommende Schrott wird mittels der zwei Schrottkörbe nacheinander in den Schmelzofen gefüllt. In der Fachsprache der Metallurgen heißt dieser Vorgang „der Ofen wird chargiert“. Nachdem die Elektrode und der Ofendeckel gehoben wurden, öffnet sich der Ofen, damit der Schrottkorb hinein entleert werden kann. Nach dem Schließen des Deckels wird die Elektrode eingefahren und der Schmelzvorgang beginnt. Dafür wird ein Lichtbogen mit einer elektrischen Leistung von bis zu 100 Megawatt gezündet. In weniger als einer Stunde bringt der gewaltige Lichtbogen den Schrott auf eine Temperatur von 1.620°C. Das Ergebnis ist flüssiger Stahl.
Der Elektroschmelzofen ist das Herzstück unseres Elektrostahlwerkes. Er arbeitet nach dem Prinzip des Gleichstrom-Lichtbogen-Verfahrens. Das Ofengefäß hat einen Durchmesser von 6 m. Der Ofenboden dient gleichzeitig als Anode. Die Elektrode, über die der Energieeintrag in den Ofen erfolgt, besteht aus Grafit und hat einen Durchmesser von 750 mm.
Unser exakt gesteuerter Schmelzprozess.
Im Stahl-Schmelzprozess müssen die Elektrodenbewegung, die Schlackenführung, der Kohlenstoff-, Schwefel- und Phosphorgehalt sowie die Rauchgastemperatur präzise aufeinander abgestimmt werden. Diese Abstimmung wird von unseren Fachleuten auf der Steuerbühne kontrolliert und gesteuert. Seitlich angebrachte, erdgasbetriebene Brenner und Sauerstofflanzen im Ofen unterstützen den Schmelzvorgang. Unerwünschte Stoffe, die beim Einschmelzen des Schrottes entstehen, werden in der Schlacke gebunden, die an der Oberfläche der Stahlschmelze schwimmt. Das während des Schmelzvorgangs entstehende Rauchgas wird über die Sammelleitung zur modernen Rauchgasreinigungs-Anlage geführt, dort gereinigt, bevor sie das Werk verlassen.
Die Stahlschmelze wird für Kundenwünsche optimiert.
Kurz vor dem Abstich wird die Temperatur des flüssigen Stahls automatisch mit einer Sonde gemessen. Sobald die Zusammensetzung und Temperatur den Vorgaben entsprechen, machen wir den Abstich. Unmittelbar vor dem Abstich fährt eine vorgewärmte Pfanne unter den Ofen. Nun neigt sich das komplette Ofengefäß, damit die oben schwimmende Schlacke in einen Schlackebunker abfließen kann. Später wird die Schlacke unter anderem zu Baustoffen weiterverarbeitet. Eine letzte Stahlprobe wird aus dem Ofen entnommen und analysiert. Dabei fließt der flüssige Stahl in die Pfanne des Stahlübergabewagens. Der Übergabewagen fährt wenige Meter vom Elektro- zum Pfannenofen. Dort wird der Stahl chemisch analysiert. Die Stahlproben entnehmen wir der Pfanne und analysieren sie im Labor neben der Ofenbühne. Innerhalb kurzer Zeit zeigt der Analyse-Monitor die Zusammensetzung des Stahls. Ausgehend von diesen Ergebnissen optimieren wir durch Zuschlags- und Legierungsstoffe die Eigenschaften sowie die Qualität der Schmelze, damit sie genau den spezifischen Kundenanforderungen an den finalen Stahl entspricht. Je nach Bedarf geben wir weitere Zuschlagstoffe in die Schmelze. Dabei sorgen die Lichtbögen dreier Elektroden von je 400mm Durchmesser für die richtige Übergabetemperatur. Gleichzeitig homogenisieren Argonspülungen die Schmelze. Sobald die Parameter des Stahls den Vorgaben entsprechen, fährt der Übergabewagen mit der Pfanne in die Gießhalle.